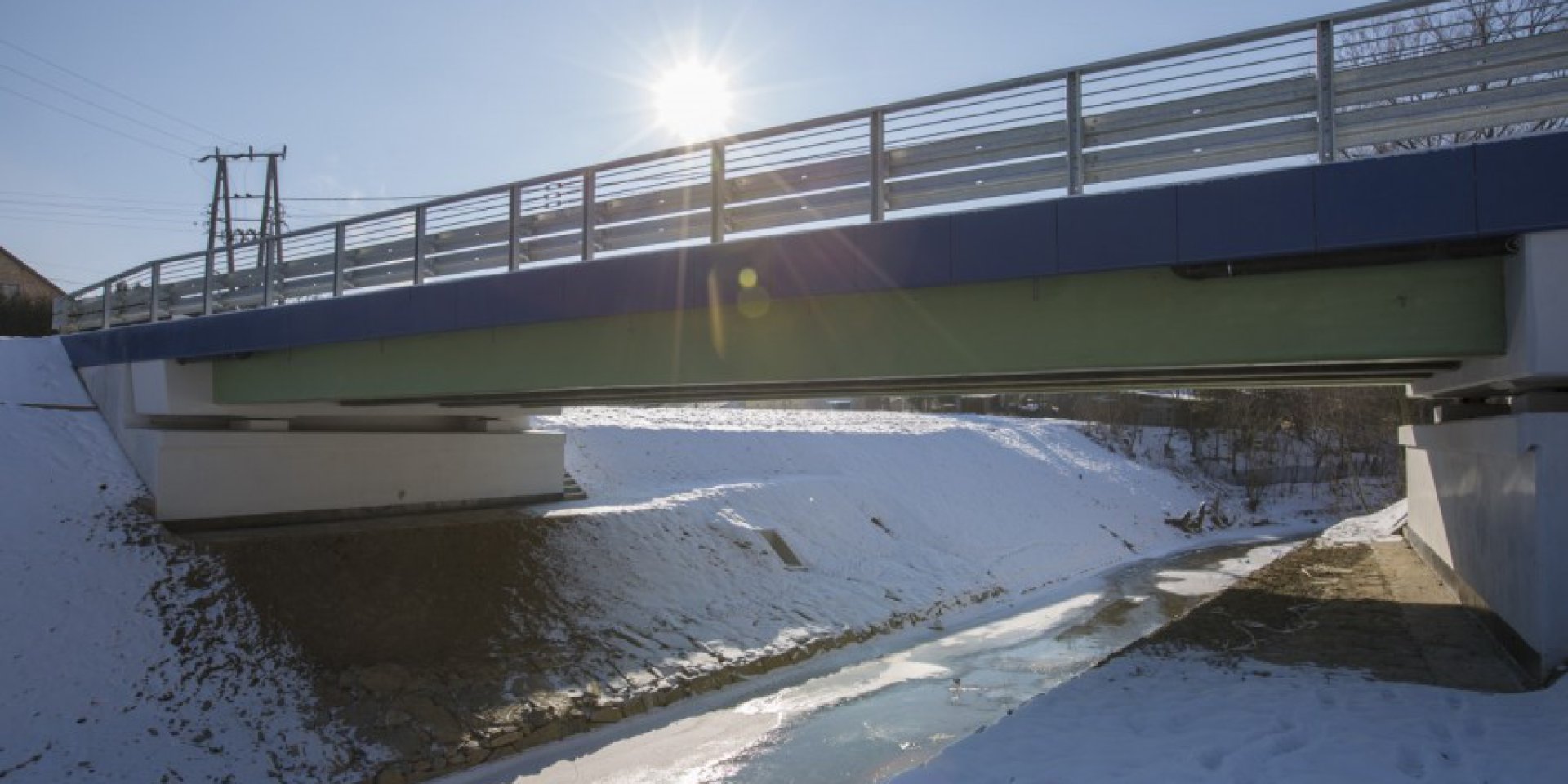
The innovative FRP road bridge
The first in Poland and one of only a few such structures in Europe, the innovative FRP road bridge is being built under the Com-bridge research project. It also marks one of the largest (in terms of span length) structures of this type in the world. The project is being completed by the consortium led by Mostostal Warszawa SA in a cooperative effort with the Rzeszów University of Technology, Warsaw University of Technology and Promost Consulting from Rzeszów. The contractors estimate that the bridge will remain in operation for 50-75 years without incurring any additional costs.
A demo composite bridge is being built as part of the Demonstrator Plus program run by the National Center for Research and Development, which has earmarked PLN 5.15 M to support the scientific research and development work for this purpose at the demo stage. The bridge, which will be co-funded from program funds, is owned by the Rzeszów Local Authority (the bridge will be built in Błażowa near Rzeszów). Research and preparation work (prefabrication of construction elements) is currently under way. Once the bridge has been built, its operation parameters will be tested. The whole project, including industrial tests, development work, and demo installation work, will last from November 2013 until March 2016.
Leader in engineering concepts
For years, Mostostal Warszawa S.A. has been a pioneer in innovation in the construction sector. The construction of a demo composite bridge is one of the results of the company's operation and its involvement in research and development. Eight years ago, it founded its own research and development department as the only company in the entire Polish construction sector. Currently, it employs several specialists in fields such as: construction, sanitary engineering, electronics and material science. They cooperate with major research units in Poland and abroad. "We are aware of the fact that by supporting new technologies we are investing in the company but – more importantly – in the development of Polish engineering. The work of our specialists has resulted in achievements such as the Com-bridge project and the construction of the first demo FRP road bridge in Poland," says Juliusz Żach, R[&]D Manager at Mostostal Warszawa SA.
The bridge of tomorrow
The demo bridge will be built alongside a road that is already in use. The current road bridge at ul. Pułaskiego in Błażowa was built in 1958. It is a steel-wood structure that fails to meet contemporary requirements. Due to its bad condition, the bridge's load-bearing capacity has been reduced to 15 tons. The project also includes design and construction work (demolition of the current bridge, construction of abutments, a span, access roads and river bank protections) as well as research work (bridge components will be tested for statics and dynamics at the lab; operation parameters of the completed facility will also be tested). The new bridge will be made of fiber-reinforced polymer (FRP). These will be carbon and glass fibers in an epoxy resin. The application of this type of material makes the entire structure a lot lighter and durable. Its superb mechanical parameters, durability and corrosion resistance have prompted the application of the composites in aviation, automobile and shipbuilding industries for many years. For the last 30 years or so, the composites have been used more extensively in construction. As regards Poland, these materials have so far been used mainly in the form of mats and tapes as reinforcement components. The project in Błażowa will therefore mark Poland's first attempt to build an FRP road bridge. It will also be one of the largest (in terms of span length) structures of this type worldwide.
A beam tailored for success
The bridge will feature a plate-beam structure. The light composite-reinforced concrete plate will be spliced with four composite girders. However, prior to making the elements, Mostostal Warszawa will first build a test beam designed for tests. The beam will be shipped to the Rzeszów University of Technology laboratory where it will be tested in detail for durability until it is destroyed. The data collected through this method will be used to verify and validate a numerical model applied in the design of bridges. Only following this stage will Mostostal Warszawa specialists initiate the production of four girders designed as the bridge's main structural component.
Investment in sustained Development
The cost of the project is estimated at PLN 10 million and it includes research work, construction of the structure as well as parameter tests. "The cost slightly exceeds the construction of a standard bridge, but by applying modern materials the construction time will be shorter and maintenance costs will be kept at a low level. The common use of FRP composites in bridge construction will surely lead to their lower cost (an analogical trend was observed, for example, in the sports or automotive sectors). However, even nowadays, despite the quite steep initial costs, the life cycle cost analysis (LCCA) shows that the construction of composite bridges is justifiable from the economic point of view," adds Juliusz Żach, R[&]D Manager at Mostostal Warszawa S.A.
Depending on the type and location of the passage, environmental and terrain conditions, required time of construction and estimated life cycle of the structure, the total life cycle cost for composite bridges are comparable to and definitely lower than the cost of structures made from standard materials.
Technical parameters of the bridge
Design span: 21 m;
Width: 10 m;
Static diagram: simple beam;
Horizontal location: straight;
Load class as per PN-85/S-10030: “B” (40 tons);
Usable widths:
Road: 2×3,5 m = 7,0 m;
Sidewalk: 2,0 m;
Shoulder: 0,5 m;
Foundation: indirect on wells (posts);
Support casings: massive concrete composite-member reinforced abutments (C30/37);
Facility drainage system: surface-type with storm water evacuated to the existing storm water drainage;
Span support system: 4 composite girders joined with light weight concrete composite-member reinforced beam (LC35/38);
Bridge deck (18 cm wide) to be completed in situ on composite sacrificial formwork;
Single beam (girder) weight: 25kN;
Girder height: 1,0 m;
Reinforcement member production method: pultrusion;
Composite beam production method: infusion;
Material applied for construction of girders: carbon and glass fiber, epoxy resin, plastic foam (as core material).
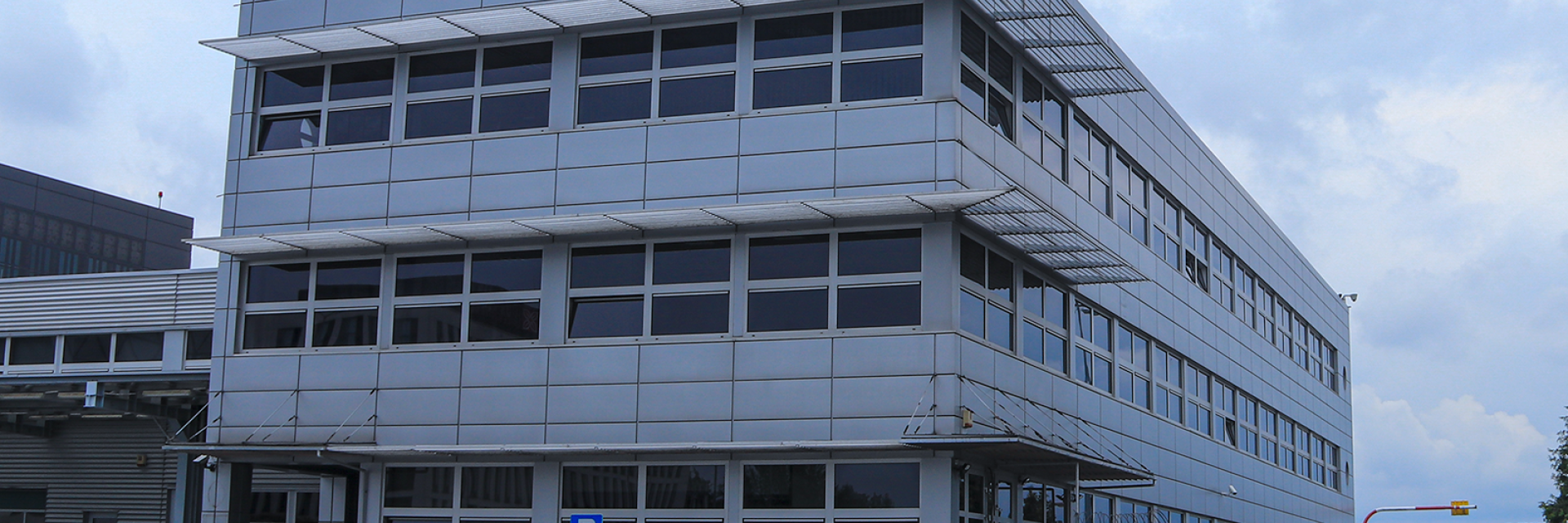
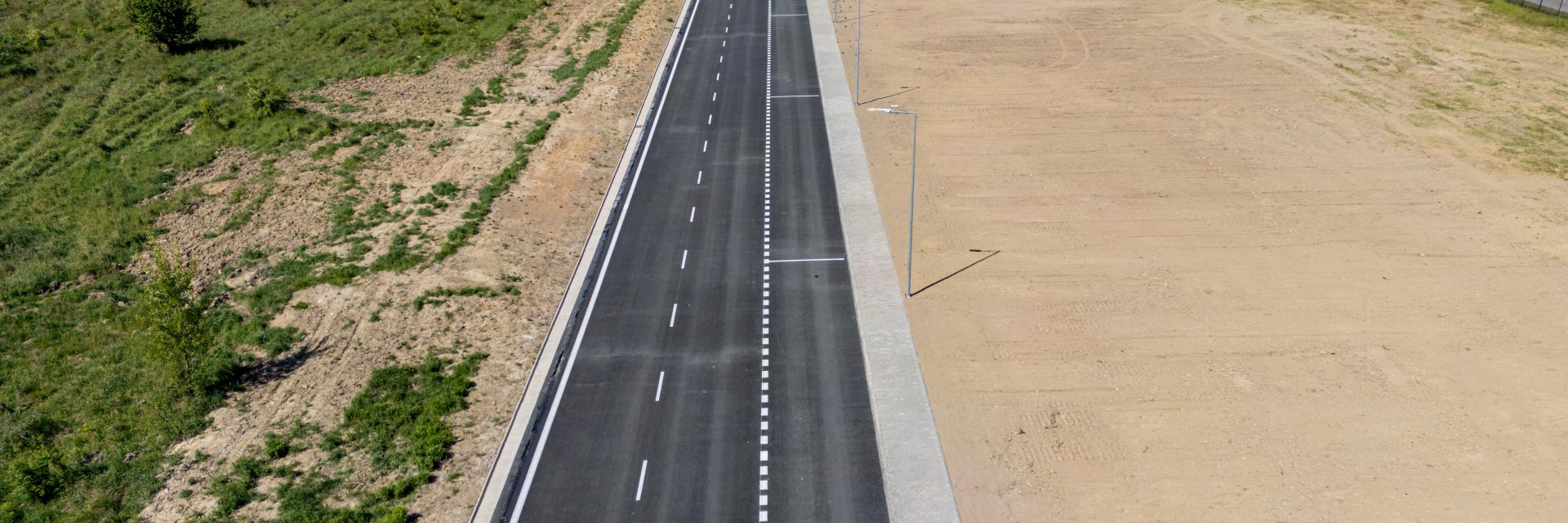
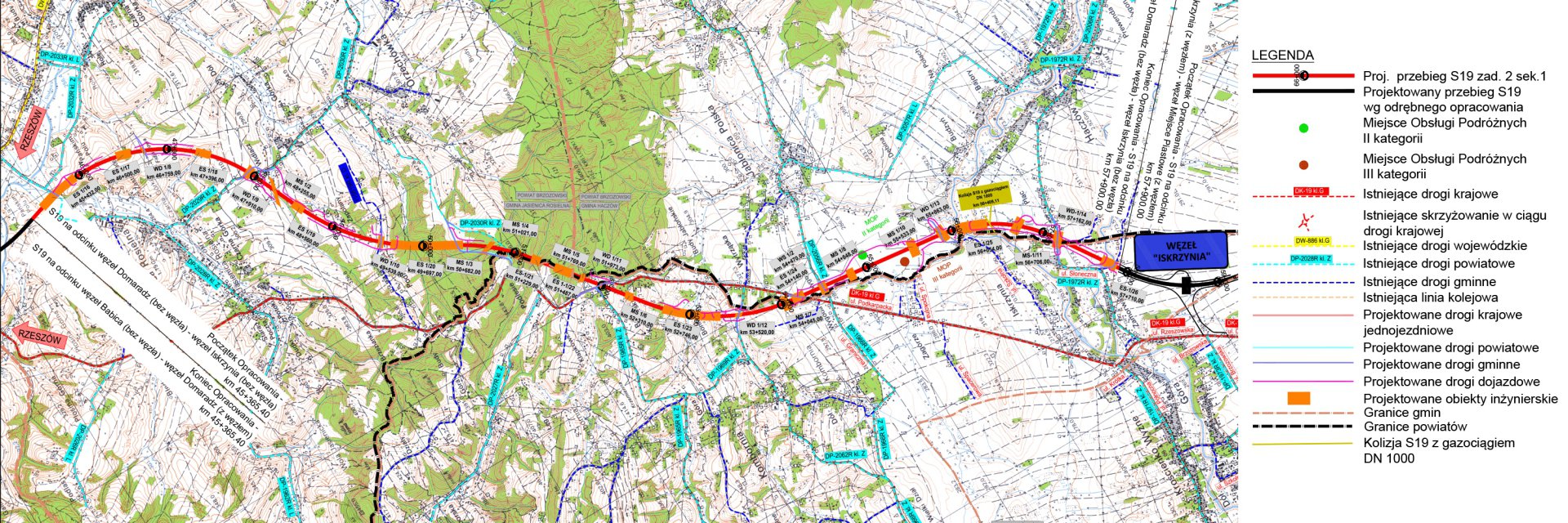
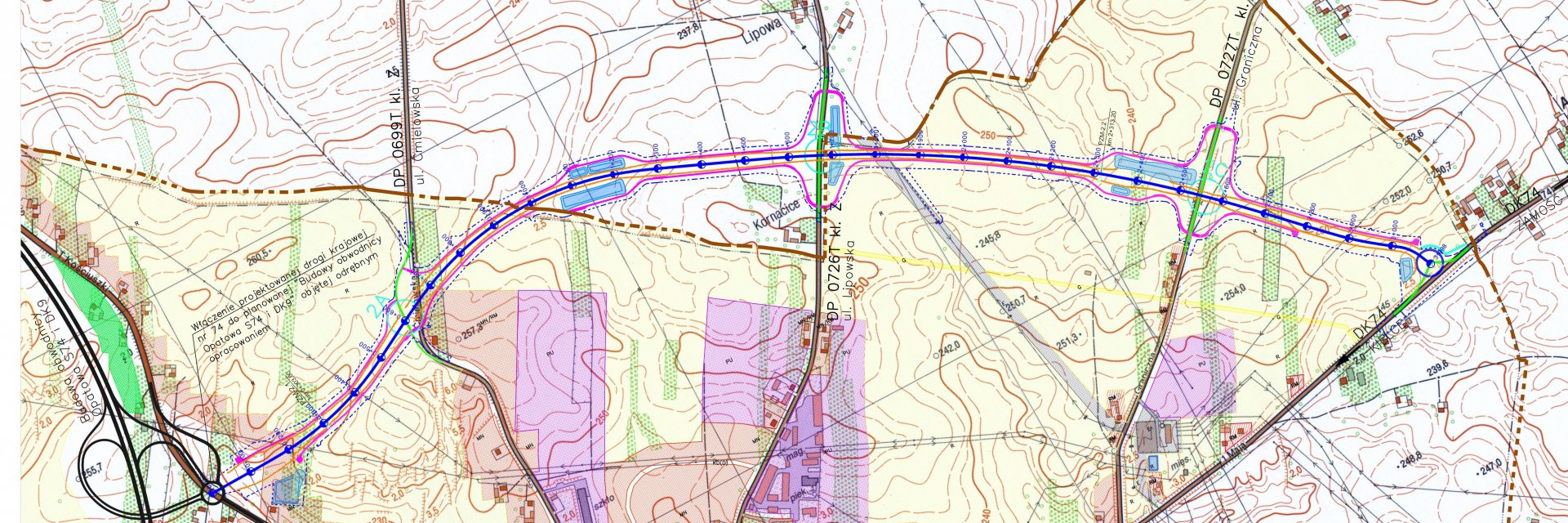
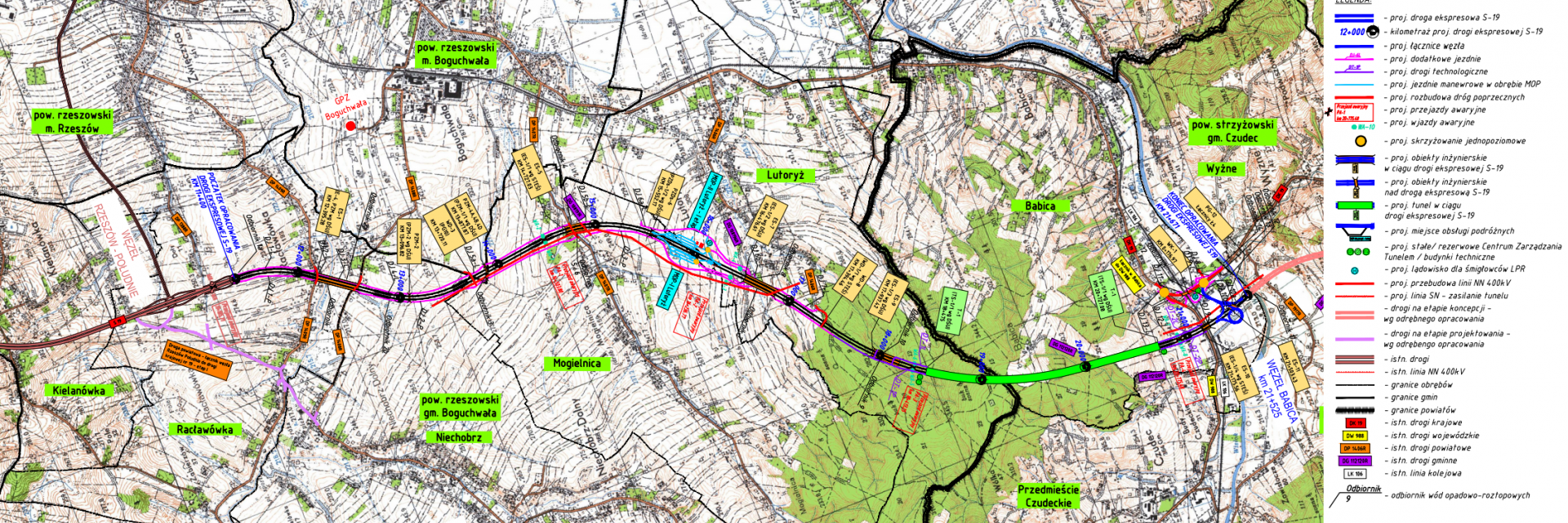
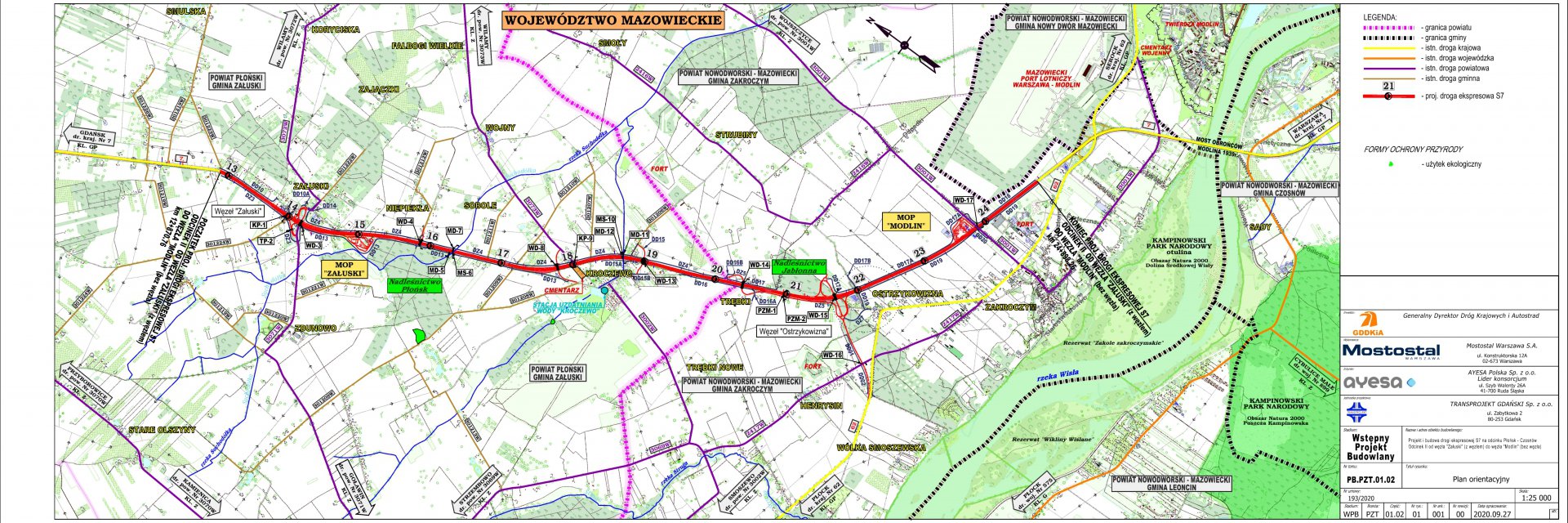
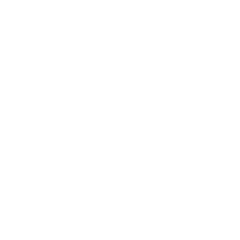